Designers are constantly imagining the future. Imagination has no limits, but the process of turning ideas into tangible objects is nested in limiting environments. At flyingshapes, we believe there is a better way. Discover how designing in VR can pave the way forward and make every stage of the design process a true reflection of the discipline’s innovative character.
Back to basics: Golden rules of design
Let’s start off by remembering Dieter Rams and his set of 10 principles for good design. One of them was that good design is as little design as possible. This prompts a question you may have asked yourself many times. What is the minimal expression of a concept that offers maximum viability?
The answer leads us to one of the golden rules of design: you can draw any iconic design using three lines – and only three. In hindsight, this always seems obvious, maybe because of its undeniable simplicity. This basic rule of design is simple in its formulation, but in real life it’s difficult to achieve. Why?
Partly because the ability to reduce a concept to three lines is a fine skill. This skill requires distilling the essence of a concept and being incisive enough to remove clutter, get rid of fog, and be left with a crisp idea.
There’s another obstacle to simplicity-driven design. Designers have limited tools to convey a concept exactly as they imagine it, and sometimes design efforts reach a dead end. In this situation, there seems to be a gap between the idea that’s finalized in the designer’s head and its final form in the real world.
Towards a new way of design with flyingshapes
We’ve seen that under the current paradigm, even the golden rules of design are limited by mediums and skills. But it’s possible to move towards a new and limitless way of design ‘ the flyingshapes way of design.
This new approach is supported by virtual reality technology at the service of design. Of course, rules still apply. When designing in VR, it’s still necessary to start with a perfect line. But technology makes this the default result by creating self-perfecting lines. Design concepts still need to be producible and scalable, but this is easier when you can work with the exact approach right from start.
In turn, this allows designers to fulfill another basic rule of design: you can enhance good design with details, but you can never enhance a poorly executed base with details. Designing in VR ensures every starting point is a solid base. It ensures you can go from mind to medium directly, with only a handful of steps in between. In short, it allows you to take the essence of the design experience and free it from constraints.
The flyingshapes way of design
Start with the idea
The starting point doesn’t look too different from the usual design process: you have an idea, then you start sketching. You draw primary and secondary lines to describe the overall design in more or less detail. Here’s where designing with flyingshapes starts to feel different. This tool allows you to value lines differently and assign a hierarchy.
This way, when you zoom out, you will always see the primary lines. You no longer need to move around a model to cross-reference it with your original idea. The virtual environment in flyingshapes gives you the stereoscopic vision you need to do that.
With practice, you can move from sketching to having a model that’s good enough to go to review in just 1 hour. The review process itself can also be completed in no time, as no preparation is required and flyingshapes allows multiple people to do live changes simultaneously. Because the feedback is so visual and so precise, you can complete change requests in as little as 1 hour.
Once you receive approval, the model is ready to go to surfacing.
Surfacing
Here you start with base surfaces, creating a handful of descriptive surfaces that show where you want to go with the design.
In an analogue process, the next step would be using clay to work on its surfaces. However, doing this means losing or covering previous data. You can only guesstimate or resort to your memory to account for that data. By contrast, flyingshapes preserves data integrity during surfacing. All you need to do is grab an end point and modify the entire surface. You never leave the chosen visualization settings, so you stay within the same visual communication space.
Once you’ve created a rough surface model, you fine-tune it based on things like light reflections. At this point, we’re entering a world of volume where scale is paramount. flyingshapes facilitates that vision, since it allows you to see realistic light simulations to better understand surface and shape.
With this tool, you can also zoom in or out to judge distance and scale. This prevents a common trap in modeling: getting lost in the scale you’re working on. As a designer, you need the ability to zoom out to keep track of primary lines and ensure the base architecture is right before you can move into other details.
This point is more important than it seems at first sight. You no longer need to figure out how to move in space. Instead, with flyingshapes you learn to move space itself. This is a powerful conceptual shift that evidences the shortcomings of the analogue design process.
The differences don’t end there. In the traditional process, design teams often struggle to decide how far to go with surfacing. With flyingshapes, you can let go of unnecessary complexity and of the constant need to judge how far is too far and whether good is good enough. Instead, you gain the ability to make a very fast assessment and know exactly when a model can be handed to tooling.
From design to execution
Tooling and engineering execution are outside of a designer’s purview, but they’re still part of the design process. flyingshapes was created to completely transform this process, from beginning to end and including its execution stages. How?
This tool features a collaborative environment where everyone can access a clear visual reference ‘ so clear, that translation and interpretation problems become a non-issue. This eliminates many of the frustrations experienced by engineering teams in the later stages of the design process.
How does this look in real life? The Porsche 914 example
Designing in VR means eliminating redundancies and translation problems. It means dramatically reducing time to market ‘ by nearly 80 % in automotive design. When designing in VR, the complexity of this design task is reduced to:
Creating a key sketch ready for review.

Creating a key sculpture in a simulated environment, also ready for review.
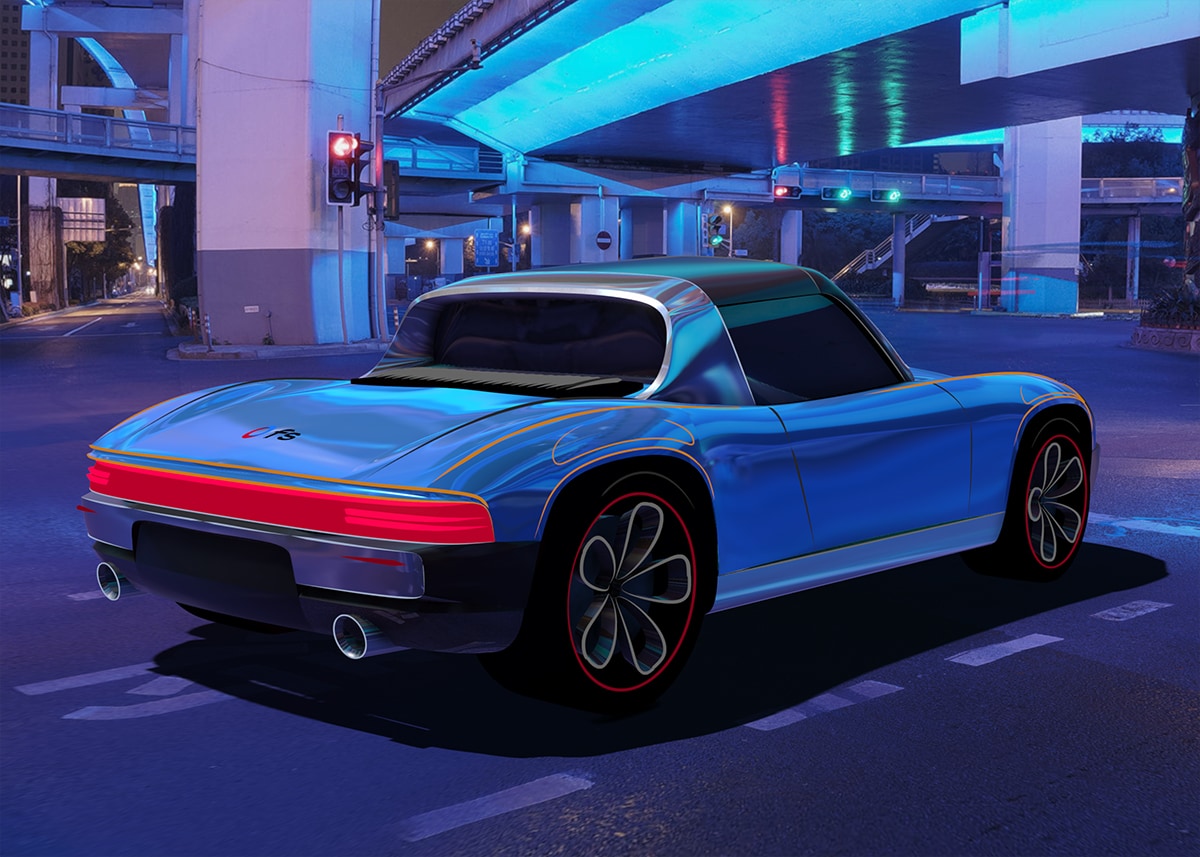
From that point, the team can move onto the feasibility gate. And a few weeks later, the car is ready for production.
This is only possible when you have a bridging tool, a mind-to-mind interface like flyingshapes. With it, an idea becomes communication and communication propels the design process forward. As a result, you can have a concept like the Porsche 914 fully validated in just 7 weeks.
VR will revolutionize the way you think about design
Designing in VR doesn’t just mean learning to use another tool: it’s a paradigm shift. A handful of hours using flyingshapes will revolutionize the way you think about design. And with that change in perception comes a shift in execution, which becomes less long-winded because quality and precision are the starting points.
flyingshapes has no counterparts in the analogue world. It’s a tool that simplifies the design process and augments the potential of your design skills. We’re confident you and your team will be impressed with the possibilities. Start exploring them today with a free flyingshapes trial.